As a composer and producer, I draw my inspiration from many different styles of music
and in many ways, my music can be seen as a combination of all these influences. For this
project, I had two very specific frames of reference, György Ligeti's 1966 choir piece Lux Aeterna and Fernando Corona's (Murcof) Oort, taken from his 2007 album, Cosmos.
These two pieces of music have had a huge impact on me throughout the years and I always find myself going back to them, trying to understand what it is that is so beguiling, mysterious and ultimately wonderful about them both.
Halliday/Fessmann
Prodject stone: Oct to Dec 2016.


bbbbbbbbb
When I first discovered the sound stones of Hannes Fessmann on his Youtube channel back in 2014, his film "A brief history about Sound and Stone" really grabbed my attention in much the same way Lux Aeterna and Oort had. I was absolutely captivated by the
strange microtonal sounds coming from these mysterious black, stone objects, they seemed to embody the sonic mystery of Lux Aeterna and Oort. I wondered if this was the instrument with which I could finally approach making some music inspired by
those two pieces.
It wasn't until Easter 2016 that I got the opportunity to speak to Hannes about the possibility of working with him. He graciously agreed and we discussed the various
ways of conducting the research. We finally settled on the concept of making my very own "project stone" which would allow me the opportunity to fully document the whole process from start to finish. I arrived in Nürtingen, South Germany in October 2016 and we started work designing the halliday/fessmann project stone.
First and foremost the project stone had to have the right sound qualities, to this ends
we spent a lot of time in Hannes's studio playing and listening to his stones trying to isolate the kind of sounds I wanted to use. I was particularly interested in the low-end frequencies of the mid sized rectangular shapes. After a few different designs and many late night discussions, we decided upon a sloping rectangle shape with very thin lamellas.
(see above) The idea behind using very thin Lamellas was to try and stimulate the maximum amount of sound and vibrations whilst keeping the stone to a smaller, more manageable size. When working with sounds stones this aspect of the process must never be under- estimated, the logistics of transporting a sound stone are problematic. A stone can weigh anything from 50 to 200kg, yet they still remain incredibly fragile. I consider this to be one of the major factors preventing the research of these instruments further afield.
György Ligeti: Lux Aeterna
Murcof: Oort

Hannes Fessmann's truck: transporting the raw stone: image source: Steven Halliday
In order to make our project stone, we had to first transport a full-sized block of Gabbro to a Stone Mason's in Tübingen,
South Germany. The block had been cut, prepared and shipped from a quarry in Tamil Nadu, South East Indian. Gabbro is the favored stone for making these instruments mainly due to its tightly compounded holocrystalline mass.
Gabbro forms when molten magma is trapped beneath the Earth's surface and slowly cools, much of the Earth's oceanic crust is made of this stone.

We arrived at the Stone Mason's early in the morning and set about cutting the full sized block in half, these two pieces will eventually become two separate sound stones. Cutting in the lamellas is a very lengthy process taking up to an hour for each one. This is all done using large diameter, laser guided, water lubricated, circular saws. These machines
are incredibly powerful and mainly used for large scale commercial projects. The process cannot begin until the stone block has been fixed to the cutting bed and measurements have been taken.These measurements are inputted into the machine's computer along with the size and depth of the required cuts. The whole process took around 15 hours, spread over two days.
Full size Gabbro block: image source: Steven Halliday
The stone cutting process: video by Steven Halliday
The next phase of the process is to polish the stone and develop the sounds of the lamellas. It is at this point that you find out exactly what notes your stone can play. Up until now, there was no way of knowing what exact notes we were going to get. Research into developing scale specific stones has begun but at this point it is still very much trail and error. Hannes uses his extensive experience to create specific tonal qualities but the exact tones are difficult to pre-define.
Polishing the stone is an essential part
of the whole process, by removing all
the sharp edges, this allows the player
to smoothly run their wet fingertips
(and palms) over the top and sides of the
stone. It is this "stick and slide" action
that produces the vibrations inside
the stone which, in turn, produces the sound. All the polishing is painstakingly done by hand, using a selection of angle grinders, sanding blocks and papers.
Developing the sounds of the lamellas is
a very delicate process that evolves over time. Similar to other instruments, the sound stone has to be "played in" over a number of months. Each lamella is played and rested, played and rested, until you eventually get a more uniformed sound.
This process can only be undertaken by a sound stone practitioner who has worked
on a large number of stones.

The polishing process: image source: Wolfgang Steche

Halliday/Fessmann project stone: image source: Steven Halliday
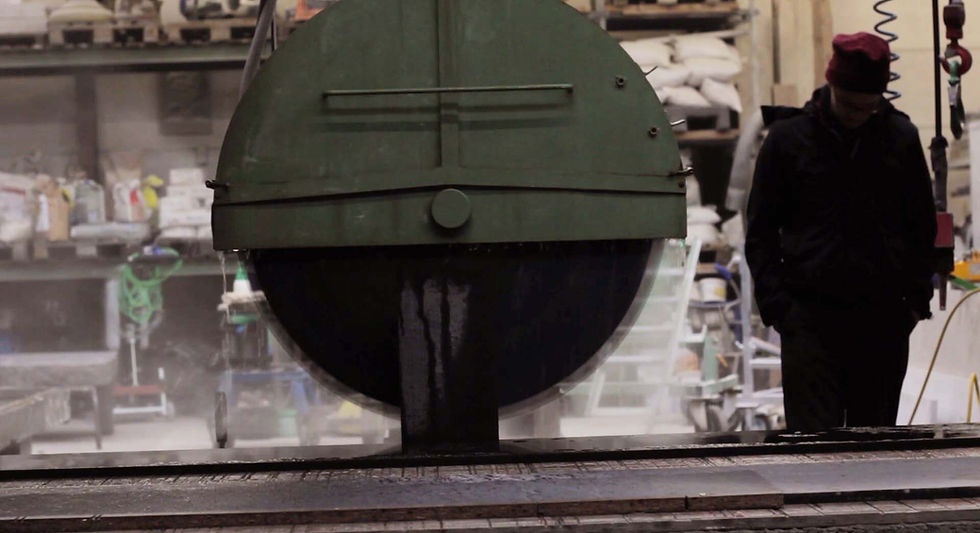